Sanitation Technologies
A Division Of Anderson Chemical CompanyEgg Industry
Anderson has served the Egg Industry for over 40 years now. We feel we can provide professional, forward looking programs that will enhance your plant operations in many areas beyond just sanitation.
Program Applications- Egg
PROGRAM APPLICATIONSShell Egg WashersAreas To ServiceMembrane Cleaning ProgramsEnvironmental ProgramsCIP SystemsSingle-Use or Self Circulating CIP ProgramsFinished Product Packaging AreasPotable Water ControlEntryway Sanitizing ProgramsManual Plant Cleaning Programs
PROGRAM APPLICATIONS
The following series of application photos highlight Anderson’s system approach to monitoring and dispensing equipment field installations. Also included are some before and after examples of process equipment that have gone through the Anderson program.
Important basics in egg facility sanitation.
- Self-circulate (HTST, shell egg washer, etc.)
Important basics in egg facility sanitation.
- Condition and microbiology of the unclean egg
- The mechanical egg washer and USDA requirements
- The process area environment
- Handling and storage of eggs
- Egg processing equipment and product flows
- Cleaning principles
- Cleaning and sanitizing products
- Reducing costs and improving the sanitation program
- Foam equipment exteriors and environmental areas (and some internals of equipment).
- High Pressure spray of equipment exteriors (and some internals of equipment). May employ Flo-Jet system with drop stations.
- Clean-In-Place
- Self-circulate (HTST, shell egg washer, etc.)
- Clean-Out of-Place
- COP Washers
- Manual Cleaning
Shell Egg Washers
- In addition to manure, blood, etc. on the shell egg, whole egg contents contaminate the wash water (and the washer unit mechanical rollers, etc.) due to cracked, leaking eggs.
- Whole egg soil is equal parts of protein, fat, and mineral.
- Built alkaline products work best in egg washers due to the nature of the soil (providing an alkaline pH with water conditioning agents to tie-up minerals).
- Surfactant defoamers suppress egg protein foam and provide improved wetting to sheet water from the egg surface. (Silicone antifoams reduce excessive foaming).
- Work to control water usage in the washer.
- Controlling water also controls:
1. Alkaline detergent
2. Defoamer
3. Sanitizer
- BTU’s
- Effluent waste water
Shell Egg Washer Checks:
- Dispensing pumps for proper operation
- Probe
- Chlorine sanitizer pump
- Dispensing lines and fittings
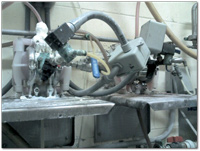
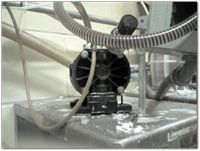
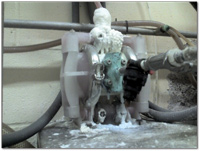
Shell Egg Washer (After)
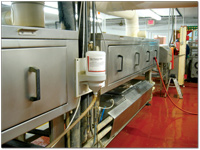
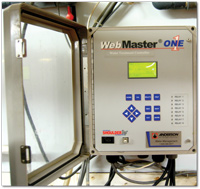
Shell Egg Conveyor To Washer
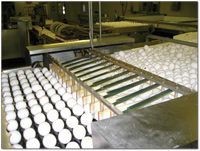
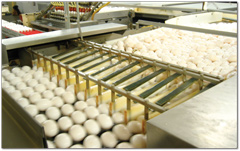
Areas To Service
Eggs must be handled appropriately throughout each phase of processing, equipment, production and packaging, etc. to preserve quality.
Processing Area/Breakers & Separating Room
The sanitary condition of the processing facility is important. The design and layout of the building and premises must provide good environmental conditions, facilitate cleaning, minimize contamination, reduce the potential for pests, and have adequate space for processing operations.
- Automatic Breakers (may be rotary)
- Breakers may operate as a whole egg machine or separate yolk from whites
- Yolk, white, and whole egg collection tanks/pots and lines
- Filters (Canisters) for each liquid egg product (prior to plates)
- Clarifier removes shell fragments from liquid egg
- COP for parts washing, disassembled short pipes, elbows, gaskets, etc.
- Breakers (may be CIP’d or foam cleaned with cups disassembled—COP tank)
- Raw storage tanks/silos (may be separate for yolk, whites, and whole egg including the lines)
- Line Circuits: Breaker lines, Raw fill lines, Raw transfer (or process or load-out) lines
- Valve clusters
- Filters - may have PDP (rotary or product displacement pumps that are CIP’d and/or disassembled and manually cleaned)
- Raw blenders (may have blending room)
- Pasteurizer (HTST)
- HTST Holding Tube
- Chill plate or press
- COP for parts washing, disassembled short pipes, elbows, gaskets, etc.
- Dryer Systems
- Dryer CIP
- Underneath equipment
- Equipment exteriors (silos, piping, etc.)
- Equipment interiors (washers, silos, breakers, piping, liquid egg contact surfaces, HTST, chill plate, etc.)
- Shell Egg Receiving (Environmental Cleaning-Walls, Floors, Ceiling)
- Cooler Storage (Environmental - including mold control)
- Liquid Egg Receiving
- Foam and/or manually clean environmental surfaces, tanker exteriors; Spray sanitize
- Parts sinks and hand wash station
- Raw tanker CIP (may have dedicated CIP system)
♦ Receiving pump, lines, raw silos
♦ Raw tankers
Production Area / Transfer Room:
- Accumulators (gathers the eggs, places them in rows to in-feed conveyors to the washer)
- Automatic Loaders (transfers eggs from trays to in-feed roller conveyor, may destack trays and separate stuck eggs from empty trays)
- In-Feed Roller Conveyors (to washers)
- Shell Egg Washers-CIP spray wash and sanitize shell eggs
- Candling (uv light)/Inspection Station
- Tray Washers (integrated into loaders to wash trays in-line and then stack them)
- Packaging Area Equipment
- Foaming of equipment including: stands, rails, underneath equipment, environmental surfaces, equipment exteriors, etc.
Membrane Cleaning Programs
Anderson can improve your membrane cleaning program.
![]() |
![]() |
BEFORE. If your program looks like this, we can automate and improve your membrane automated chemical dispensing and control performance. | AFTER. Anderson designs and installs systems to reduce labor, improve results and consistency, while lowering overall membrane system operating costs. |
- Membrane Filtration Systems
- Reverse Osmosis and Nanofiltration Systems for concentration
- Egg white or whole egg may be concentrated (water is a main component of the egg white,
in addition to protein)
- Membrane CIP
- CIP with protease-based products
- High quality of cleaning is critical to the process
Environmental Programs
.jpg?1409782860)
Foam Cleaning Programs are available to meet
all of your plant's needs.
![]() |
![]() |
BEFORE. This picture shows egg conveyor/cartooning environmental area before cleanup. | AFTER. This picture shows conveyor environmental area after cleanup. |
CIP Systems
![]() |
![]() |
BEFORE. Does your CIP “control” look like this? We can take a look at your system, analyze the system with a trained team of experts, and work with you to provide the level of CIP control you require. | AFTER. CIP performance using Anderson custom-designed equipment will fine-tune your CIP chemical control, providing you with optimal cleaning and sanitizing results. |
- CIP product dispensing pumps for proper operation
- Conductivity readings/data versus setpoint
- In-line probes do not require physical check unless conductivity is not controlled properly
- Acid sanitizer pump
- Dispensing lines and fittings
Single-Use or Self Circulating CIP Programs
![]() |
![]() |
BEFORE. Shown here is an egg facility HTST/holding tubes. To reduce labor and improve results Anderson automated the dispensing and control of CIP cleaning program from labor-intensive to a push of a button. | AFTER. A new automated system provides a better standard of control and operation. |
Potable Water Control
Anderson provides the latest in safe, highly efficacious chlorine dioxide technology. Chlorine dioxide will improve your potable water program versus chlorine. We have improved COW water control from TNTC (out-of-control) to consistently <10 cfu/ml.
AFTER. Anderson’s systems are safe, easy, effective, and economical.
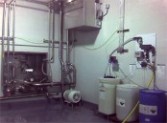
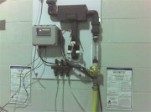
Entryway Sanitizing Programs
![]() |
![]() |
BEFORE. Entryway Foam or Floor Mat Footwear Sanitizing – Do your results look like one of these – tracking dirty water or having a poor foam mat with little to no coverage? | AFTER. Anderson can improve your facility entryway bacterial barrier with the latest technology giving you the best sanitizing performance and surface coverage possible. We have new and innovative foam sanitizing products, complementing the equipment technology. |
Manual Plant Cleaning Programs
![]() |
![]() |
BEFORE. Do you need improvements in your environmental and equipment exterior cleaning and sanitizing? We can transform a disorganized labor-intensive practice to “Best Practices”. | AFTER. This is one small example of Anderson’s manual chemical dispensing system improving operations on the plant floor. Anderson custom design-builds equipment for your facility. |